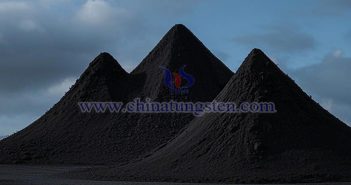
Common preparation methods for tungsten disulfide (WS?) from CTIA GROUP LTD include chemical vapor deposition (CVD), mechanical ball milling, hydrothermal synthesis, and sol-gel methods. These processes involve various preparation parameters such as reaction temperature, reaction time, reactant concentration, reaction atmosphere, and catalysts. So, how do these preparation parameters affect the properties of WS? from CTIA GROUP LTD? 1. Reaction Temperature Impact on Crystal Structure: Temperature is a critical factor influencing the crystal structure of WS?. At lower temperatures, WS? with…