Specific surface area refers to the total surface area per unit mass of a substance, typically measured in m2/g or m2/kg. For ammonium metatungstate (AMT) powder, this includes not only the external surface area of the particles but also the surface area of internal pores, cracks, and other microstructural features. This parameter directly reflects the degree of dispersion and surface activity of the material—finer particles or greater porosity result in a larger specific surface area.
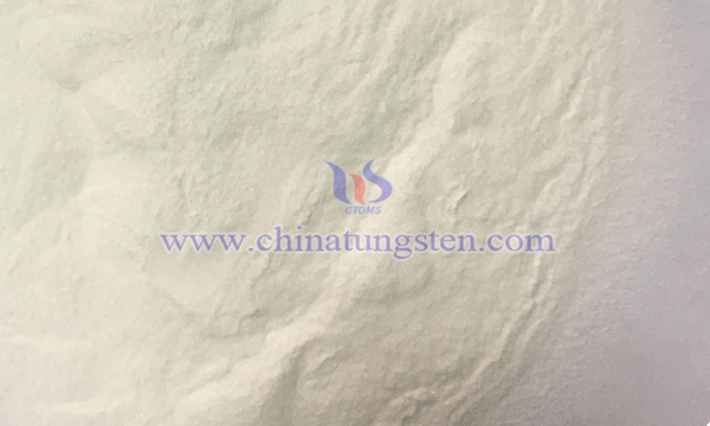
CTIA GROUP LTD AMT image
As a key intermediate in the tungsten chemical industry, AMT’s specific surface area is closely related to its crystal structure, particle size distribution, and agglomeration state. For instance, a high specific surface area indicates finer particles or more developed pores, which can affect its dissolution rate in solutions and its loading capacity as a catalyst support (e.g., in petrochemical catalysts, a larger surface area provides more active sites). When used as a precursor for energy storage materials, the specific surface area influences the electrochemical performance of the final product, such as tungsten oxide nanomaterials.
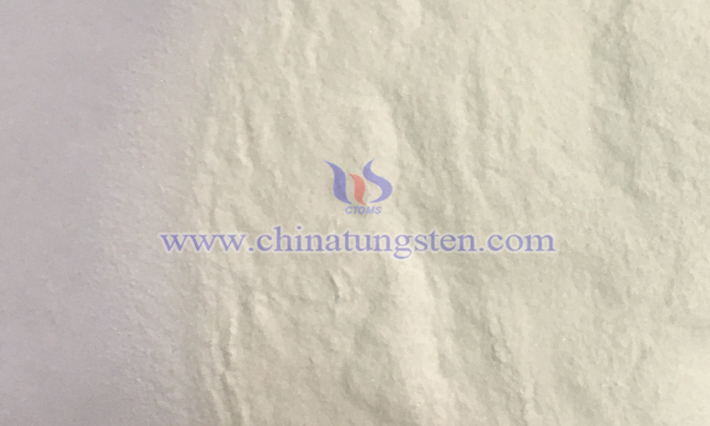
CTIA GROUP LTD AMT image
During preparation processes like precipitation, crystallization, and drying, changes in AMT’s specific surface area can indicate process stability. For example, excessively high drying temperatures may cause crystal agglomeration, reducing the specific surface area. Different applications require varying specific surface areas for AMT: ceramic material additives need a moderate surface area to ensure sintering performance, while catalytic applications may demand a high surface area to enhance reaction efficiency.
Factors influencing AMT’s specific surface area include preparation processes and post-treatment conditions. In the precipitation method, reactant concentration, pH, and temperature affect crystal growth rate, thereby impacting particle size and porosity. High-temperature calcination during post-treatment can lead to crystal sintering and agglomeration, decreasing the specific surface area. Mechanical grinding can break up agglomerates, increase surface defects, and raise the specific surface area, but excessive grinding may introduce impurities onto the particle surfaces.